Our services
Iron ore production services
Iron Ore Reserve has been estimated under Proved and Probable Category. Total geological reserve of iron ore is 41235572 T and mineable reserve is 33973835 T.
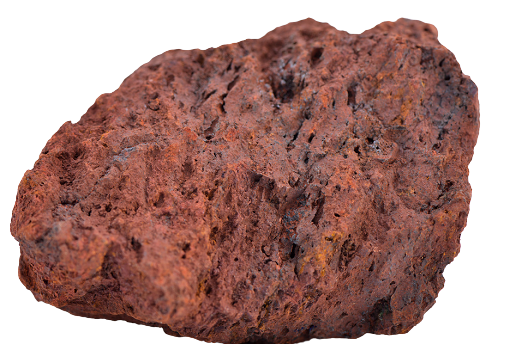
Mineral Processing
The average grade of iron ore is 58% Fe with bulk density of 3.0 T/m3 and the cut-off grade is 55% Fe. In the mining lease area, geological reserve (+58%Fe) is 60% with respect to total Iron Ore Zone. A small part of run-off mine hard massive ore produced from the mine is/will be broken into required sizes manually by the hammers and through mobile crusher. Metallurgical ore will be prepared in +10-30mm, 5-18 mm, lump/calibrated ore, lump and -5mm fines. Remaining major part of iron ore will be screened & sold to the consumers as per demand.
MINING
In the earlier approved Scheme of Mining it was proposed to develop both Raikela quarry in South Eastern part and Tantra quarry in North–East & western part simultaneously. It was proposed to develop from bottom to top towards rise side of the hill. The generated waste was proposed to dispose off on the existing dump located in south eastern part. Which is already been stabilized.
Earlier Scheme of Mining was approved by Other Than Fully Mechanized Method. This Scheme of Mining has been prepared as Fully Mechanized Method (FM).
USE OF MINERALS
Iron ore mined out from the lease area is utilized mainly for sponge iron making after sizing manually as well as by the mobile screens. Presently, iron ore is supplied @20,000 t/month for captive use in 2 kiln x 100 TPD captive sponge iron plant of M/s Seven Star Steels Ltd. located at Kelendamal, PO : Gudigaon, Jharsuguda, Odisha for production sponge iron @60,000 t/annum. Three Directors namely (1) Mr. R.L Bathwal, (2) Mr. N.K. Bathwal and (3) Mrs. Poonam Bathwal of the Lessee, M/s Penguin Trading & Agencies Ltd are common with the Directors of M/s Seven Star Steels Ltd. And also 5000t/month for captive use forsponge iron plant for M/s. Bhagabati Steel Pvt. Ltd., IDCO – plot no – 5, Industrial Growth Center, Badmal, Jharsuguda (Odisha). In addition to this, iron ore is supplied
MINERAL BENEFICIATION
A small part of run-off mine hard massive ore produced from the mine is/will be broken in to required sizes manually by the hammers and through mobile crusher. Metallurgical ore will be prepared in +10-30mm, 5-18, lump/calibrated ore, lump and -5mm fines. Remaining major part of iron ore will be screened & sold to the consumers as per demand. Water sprinkling is/will be done by a water tanker regularly in & around the screening site for dust suppression. Lumps and fines are/will be dispatched through trucks after weighing as per the demand of the consuming industries. There is a proposal to deploy mobile crushers in the lease area for breaking/crushing of hard ore. Since the capacity of the mine is enhanced from 378,360 t (1st year) to 1,080,000 t (5th year) in scheme period, operating schedule of the crushing / screening plants.
Production Process
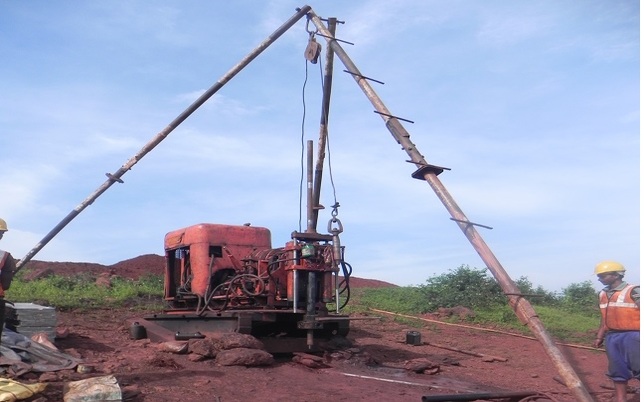
Drilling, Mining
DTH as well as jack-hammer drills are used for blast / shot hole drilling. Mining is done both by manually and mechanized means. Ten (10)/(20) tones capacity trucks/tippers are used for ore/waste transportation. Now to avoid short Hole drilling & blasting we are engaging Rock-breaker to avoid secondary blasting.
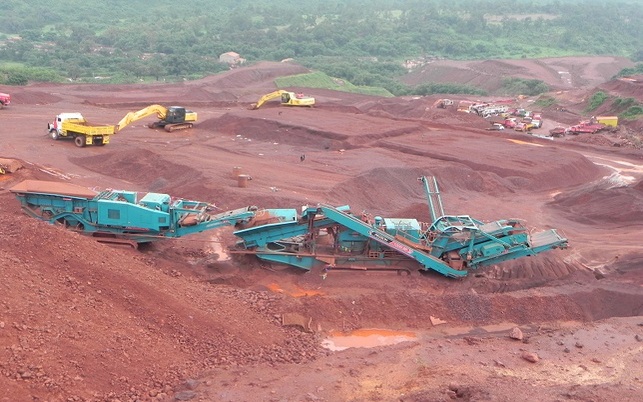
Crushing / Manual Dressing
Run-Off Mine Iron Ore boulders obtained from the face after blasting is hammered manually for sizing. Sized ore is stacked separately and loaded in tipper mechanically. In addition to this, mobile Crusher Plant and Screens are used for separation of ore from waste in to various sizes.